Pyrolysis Technology
Pyrolysis Process
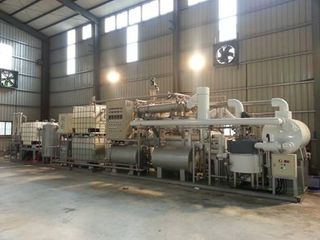
System consist parts
* Auto Feeder
* Catalytic Cracking & Pyrolysis Unit
* Heat Exchange & Cooling Unit
* Fractional distillation Unit
* Heating devices & electric control Unit
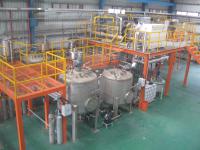
Oil Output Produced
* Gasoline: Octane number 90~93
* Diesel: Premium ~ Super
* Diesel: Sulfur less than 50ppm
* Diesel: Cetane greater than 2%
* Distillation 95% Vol Point 340 degree C
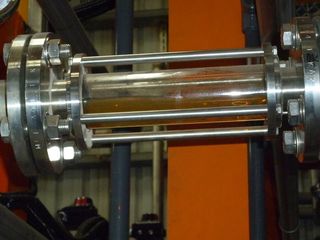
Best Quality Oils
* Excellent Volatility - easy start in winter
* High Anti-explode Capacity
* Excellent Stability
* Excellent Corrosion Resistance
* Engine will operate normally in high anti-explode capacity
Plant Main Features
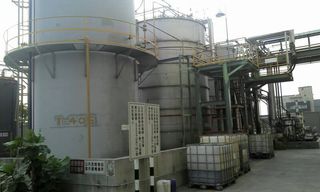
Quality
* Remove Smells- Eliminates oil product smells by utilizing special cleaning filters and detergents.
* Residue management- Skygood technology can manage residue particle sizes over 1000 mesh and can be recycled as fuel or used as filler.
* Residue processing unit- Residue processing at high temperature (300C) enables continuous production possible.
* Site safety- closed and clean production process.No second pollution
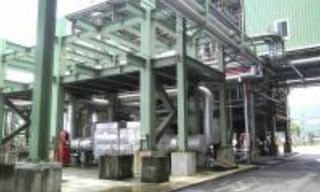
Efficiency
* Gas Recovery system- Safe, reliable, stable and uncomplicated structure.
* Auto feeder- The raw material is fed continuously by a variable pitched screw automatic compression, exhausting, dehydrating and pre-heat can be carried out during this feeding process. The small waste pieces of raw material does not require to be brocken up or cleaned.
* No cleaning or sorting of raw material
*Fully automatied operation- high efficient 24 hour operating capability.
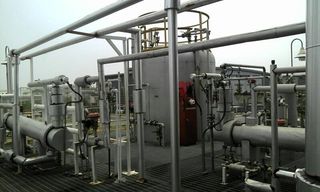
Fair Prices
* Highly Efficient Catalyst- Many catalytic reactions are involved in this sophisticated process. The exact calculation and control on the speed rate and feed ratio prevent catalysts from being damaged by toxic pollutions.
* Innovation- Catalytic pyrolysis occurs at low temperature (<280C). This offers a very high yield and conversion with fuel content greater than 80% and gas less than 5%.
* Wide range of raw materials- average conversion rate > 70%, Diesel up to 90%.
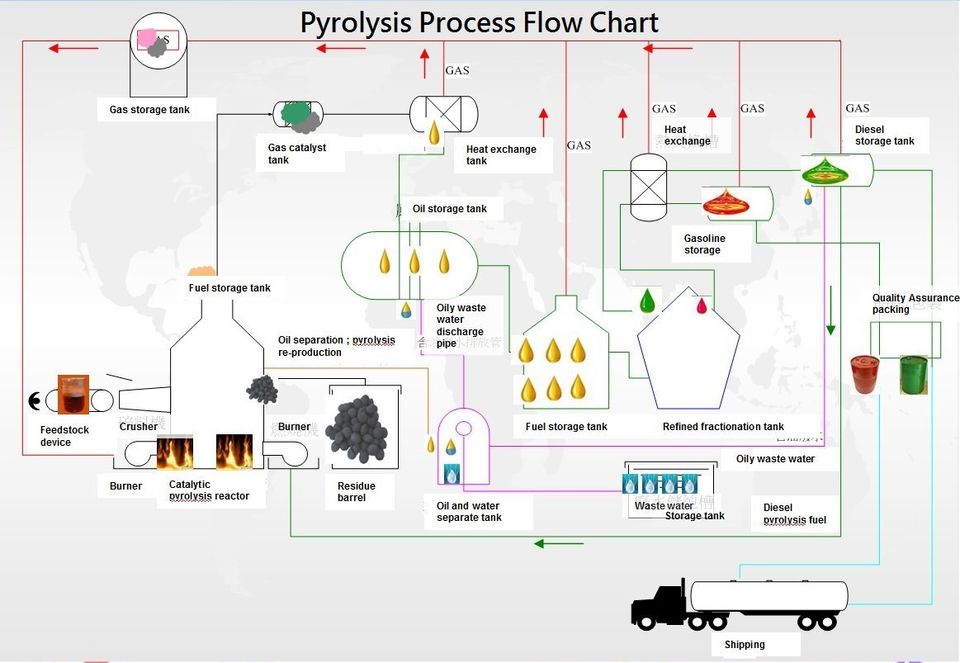
The process is used heavily in chemical industry, for example, to produce charcoal, activated carbon, methanol and other chemicals from wood, to convert ethylene dichloride into vinyl chloride to make PVC, to produce coke from coal, to convert biomass into syngas and biochar, to turn waste into safely disposable substances, and for transforming medium-weight hydrocarbons from oil into lighter ones like gasoline.
These specialized uses of pyrolysis may be called various names, such as dry distillation, destructive distillation or cracking. Pyrolysis is also used in the creation of nanoparticles, zirconia and oxides utilizing an ultrasonic nozzle in a process called ultrasonic spray pyrolysis (USP).
Retrieving Plastic Waste Material ( LDPE, HDPE, PP, PS...), Waste Tires, Biomass Waste from Landfills or MSW site. It can also apply to recycle waste plastic bags, waste oil, Lignite, brown coal and MSW biomass waste (agricultural waste and refuse, wood waste, wood-based residues, energy crops short-rotation crops, sweet sorghum, …etc.).
We can design to hot melt previously crushed or regrind waste plastic to about a one inch size particle (smaller the size - better the efficiency. After crushing, the waste plastic is then sent to the pyrolysis plant.
Waste Plastics, Biomass Waste Automatic Continuous Pyrolysis Fuel Plant
The Skygood plant needs to be installed in an industrial zone and has to meet all the advanced countries’ environmental protection emission standards. The pre-screening waste plastic, biomass waste is converted by pyrolysis process and conversion rate is about 70 percent (cracking and refining the burning oil, unleaded petrol, diesel, gas and other valuable co-products such as carbon black, crude asphalt, coke valorization and construction aggregates ).
Regarding the biomass syngas obtained from pyrolysis process not only can be utilized for internal combustion engine for electric power generation, but also can be utilized for boiler or hot-blast furnace to produce steam or hot air for drying. The gas also can be lead to tornado type dust collection tank (with stainless quality ) then send to gas burner generator system to generate the power.
Power: 0.5M-5M Watt depending on upon quantity.
Waste Plastic Pyrolysis Production line: We can provide various capacity pyrolysis plants - daily processing feed stock of 2 tons, 5 tons, 10 tons, 20 tons, 30 tons, 50 tons or two lines of 50tons make it 100 tons continuously.
Pyrolysis Major Systems:
- Feeding System
- Feed Stock Preheating System
- Pyrolysis System
- Catalytic Cracking system
- Preheating Condensing System
- Fuel oil Heat Exchange System
- Fractionating System
- Fractionating Condensing System
- Fractionating Precipitation system
- Air, Water Purify System
- Piping System
- Electrical Control System
This equipment has a very low maintenance requirement - no cleaning or sorting of raw materials which reduced labor cost, and uses an automatic conveyor feeding system fully automated operation, high-efficiency and 24 hours operating capability. Site safety, closed and clean production process. No second pollution. Wide range of raw materials, high conversion, average conversion rate > 70%, Diesel up to 90%. While one side feeds the waste plastic, the other side is supplying oil and de-slugging.
Pyrolysis Process
The shredded plastic waste is automatically and continuously fed into the pre-heating process; the plastic waste melts at this stage, PVC as it has a low melting point will crack first and the HCL will be removed in this process.
After preheating, the melted plastic is fed into the continuous cracking furnace. The cracking furnace has a solid mesh and is cyclically heated to ensure the waste plastic is completely converted by the pyrolysis reaction. Any residues are removed automatically from the cracking furnace to ensure nontoxic operation.
The pyrolysis gas fractionation and subsequent cooling from the fractionation tower, produces light and heavy oil fractions and a small amount of non-condensable gas. The light oil fraction (light gasoline) is separated and the heavy oil fraction is fed into the re-boiler and re-processed by secondary catalytic cracking.
This process produces a high-quality automotive diesel. The non-condensable gas from this purification system is used as the fuel to heat the pyrolysis system and the whole process is self-sufficient. The process by the purification system achieves all developed countries’ emissions standards.
Equipment technique:
The plant uses continuous reacting bed pyrolysis technology - the shredded recycled waste plastics is fed continuously into the cracking furnace to increase thermal efficiency and maximize processing power.
In the preheating stage, the pyrolysis plant process purifies the mixed waste plastic PVC material and harmful gases such as HCL gas are removed, this in turn protects the equipment from erosion. Inside the Pyrolysis plant the gas is fed into catalytic converter then cracked, fractionation, cooled and separated.
The non-condensable gas is purified and supply for the heating process and production use, the generated flue gas purify again by the flue gas purification system to meet the developed countries’ emission standard.
The cracking pyrolysis system produces carbide and is fed onto a conveyor system to the combustion furnace for combustion and removal. The generated harmless ash is automatically collected and is environmentally cured.